
Ever wondered what goes into transforming a family heirloom into a modern classic? Jewellery remodelling gives a new lease of life to old jewellery by turning it into something fresh - like a ring, pendant or earrings.
It's actually an extremely involved process, with many intricate steps and techniques.
I often get asked to share insights into what goes on behind the scenes, so I decided to bring you along with me on a recent bespoke remodelling project that saw me turn a bride-to-be's old gold and silver jewellery into a contemporary wedding ring for her big day.
So put the kettle on and prepare for a crash course in remodelling!
Here's what we'll cover:
A bride with a vision
Our story begins with a bride-to-be who gets in touch with me via Instagram.
She is getting married and has seen my work online and loved the look of it. So, when it came to picking out a wedding ring, she wanted to do things a little differently.
With some old jewellery lying around unworn, she wants to explore the possibility of using the diamonds and precious metals to create her new wedding band.
To kick things off, we email back and forth discussing what she has in mind and how I might be able to help.
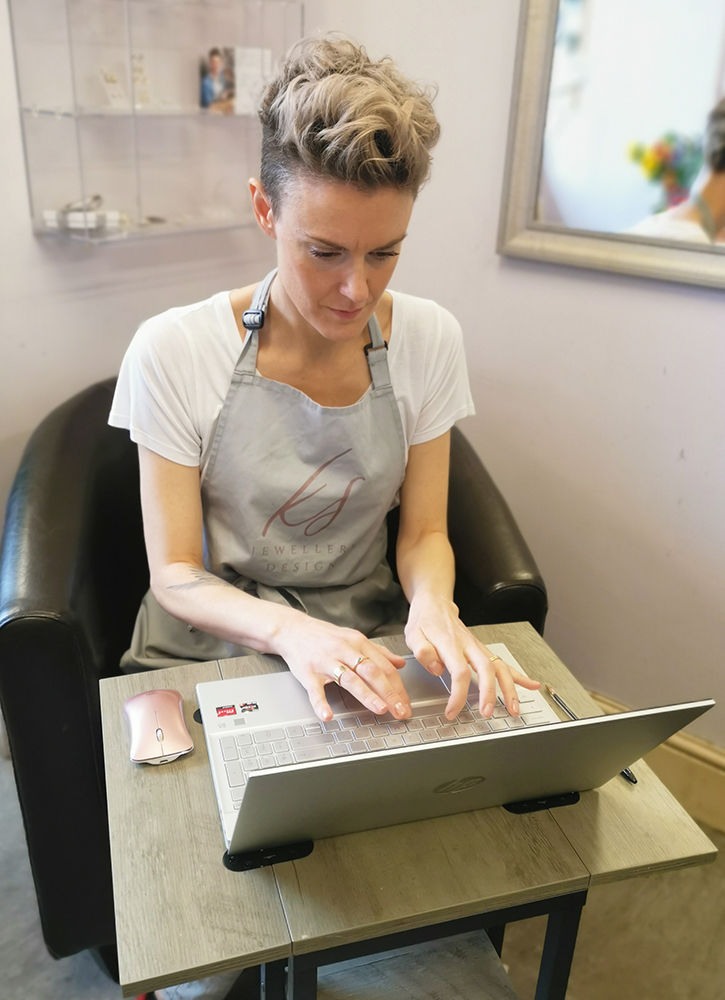

Once she's happy to get the wheels in motion, my client posts all of her jewellery to me.
Sidenote - Did you know you can do this really safely and it's insured and tracked?
We've been doing this with customers for years and we know it feels nerve-wracking to pack off items that hold sentimental value, but it's a safe way to get your pieces to me - especially if you're not local to my studio in Birmingham's Jewellery Quarter.
My client raids her jewellery box and sends me various pieces, including a diamond ring, silver jewellery that includes some bangles, old engagement rings and other items she doesn't wear anymore.
Ready to remodel: seeing old jewellery with new eyes
With the client's old jewellery safely delivered to my studio, it's time for me to get my loupe out and take a closer look!

A loupe is a small magnifying glass used by jewellers to examine pieces up close. I use it here to look for hallmarks (the quality stamp for jewellery), classify the pieces in different carats, and examine the gemstones.
My customer wants an 18ct yellow gold wedding ring, and the heirloom jewellery she sent was a mixture of different carats, so I take this into consideration when I'm investigating which pieces to rework.

After careful examination, these are the two pieces I decide to use from the selection she sent for the new ring:
From here, it's time for me to remove the gemstones from these two rings ready for them to be used in the reworked ring.
Once removed, I can measure the gems properly - taking accurate measurements is critical for me to decide on the design I can create for the customer.
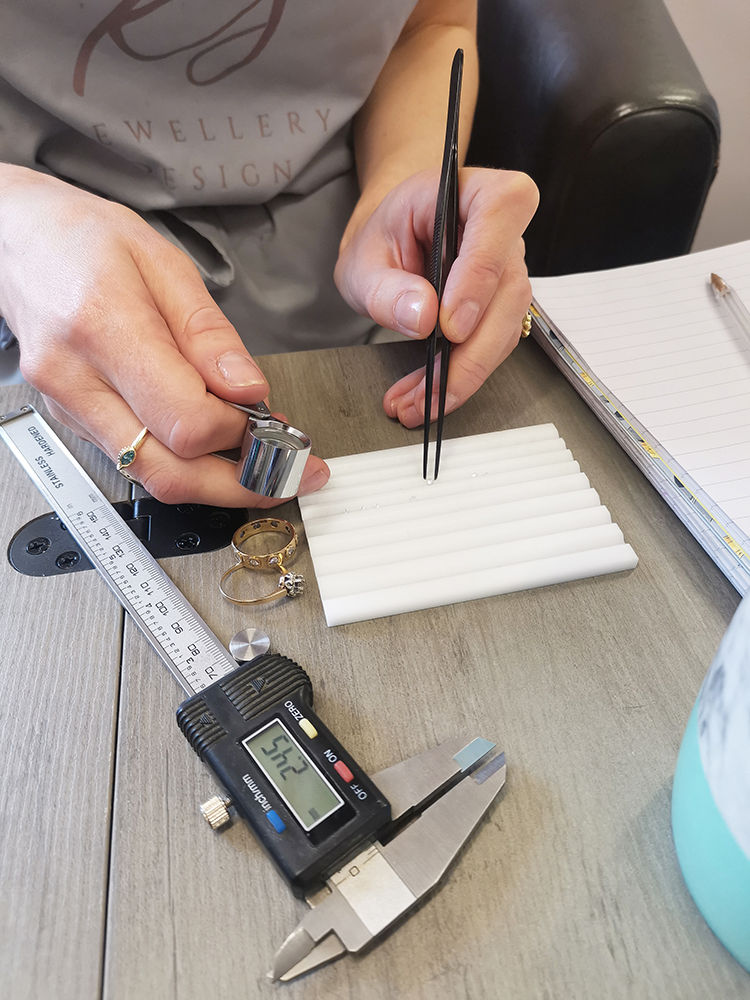
Choosing a design for the new ring
I email the customer to let her know which of the rings and gemstones I'd like to reuse - she's happy for me to scrap the rest and use the money to offset the cost of her new ring.
Now it's time to get creative!
There are endless possibilities when it comes to creating bespoke jewellery out of an original ring or rings.
So where do we begin with designing the ring? It all starts with the customer.
She likes my Dune Collection of elegant jewellery inspired by the sea, so we look over the pieces together and decide on a bespoke yellow gold ring based on one of the Dune range.
Bringing the vision to life
Up until now, it's been just me and my customer involved in the process, but I have a small team of trusted specialists who all play to their strengths to facilitate the different stages of my jewellery remodelling service.
First up is Jack, my CAD (Computer Aided Design) guy!

Jack and I work very closely to bring a raw idea into a visual representation of the finished product using 3D CAD design.
We actually do this remotely, which works amazingly well! As we've worked together for years, Jack knows exactly the aesthetic I'm after - in fact, he helped create the Dune Collection with me during lockdown.
Sharing our screens, we work together in painstaking detail ("Can you move that 1mm across?") until we have a design I'm happy to send to the client.
Jack sends me a fancy-looking 3D view of the ring that I share with my client - she clicks a link to view the image on-screen and can even rotate it 360 degrees to get a really good look at it from every angle!

Feedback on the first design
My customer has emailed me back after checking out the 3D render Jack and I created on-screen.
She says: “I love the overall aesthetic of it, I'm just not sure about the placement of the stones - could you give me another option?"
Feedback is an absolutely essential part of the process, because it's got to be 100% right for you.
Having read the feedback, I actually agree with her and ask her to leave it with me to do some refinement.
It's time to create a new design using the foundations we've built so far!
I hop back on a video meeting with Jack and we move the stones around until I feel they're in exactly the right place.
Doing this actually creates a bit of a different feel to the piece and I feel even happier with it - so I'm excited to send it back to the client to see if we've hit the nail on the head this time.
Her response?
"Yep! I love it!"
Jewellery remodelling is always a collaborative process. I'm the jewellery expert, but you're the one with a vision and a life of daily wear ahead of you - so together, we keep talking until you're over the moon with the design.


In this instance, I ask Jack to send me a 3D version of the ring in resin. This isn’t
always necessary, but I want to handle this one, get a feel for the scale and check the dimensions to make sure everything is exactly how we want it.
Jack pops it in the post to me and needless to say, I’m delighted with it!
Shopping for gems
I’m back out of my workshop next for a fun stage of the process - gem shopping!
Our remodelled pieces can use existing stones from an original piece, new stones, or a combination of the two.
Although we’re using the client’s diamonds, she wants to add an additional stone.
So, off I go to my local gemstone supplier. They're located a short walk from my studio in the Jewellery Quarter and can always be relied on to supply new stones for every occasion!
Casting the metal
With our finalised design and the all-important extra gem secured, I package up the metal that's going to be used in the ring to take it to my next specialist - the caster.
Our client's gold is going to be melted down together and formed into the new ring.
I use this particular casting company for my remodelling work because they cast using the customer’s metal only.
Generally, casting companies will cast lots of people’s work altogether so there’s a larger quantity of metal that’s distributed across everyone’s models.
This doesn’t work for my remodelling clients, as they want reassurance that only their metal has been used in their finished piece.
And it’s just as important to me!
You can rest assured nobody else’s metal is going into your ring unless we have to add metal to make it up to the correct amount of weight we need - but that’s a conversation we’ll have early on and the metal will come from my workshop, so you’ll still know exactly what’s gone into your piece.
So, with the customer’s metal packed up, I get my coat on again and head off to the casting company.

Here, the first step is for them to create a mould around the 3D-printed ring. An individual can is used, and the wax print is attached to the base of the can using what's known as a sprue - a wax rod that creates a feed which the molten metal will eventually be poured into.
Investment powder is combined with water to create a mixture very similar to plaster of Paris, but one that's able to withstand much higher temperatures and pressure.


This is poured into a can, containing the wax ring. Once the investment has set, the can is placed in a furnace. This will melt the wax model away - leaving a negative ring-shaped space!
The sprue is removed and the casting is carefully checked to make sure it’s perfect.

The gold ring is now back from the casters. But it’s far from finished - it needs skilfully working on to refine it. You can just about see where the sprue was once attached on the inside of the ring, at the back.
Cleaning up the ring
To clean up the rough version of the ring that I’ve had back from the casters, I get to work removing the sprue from the ring (the channel that fed the molten metal into the mould during the casting stage).
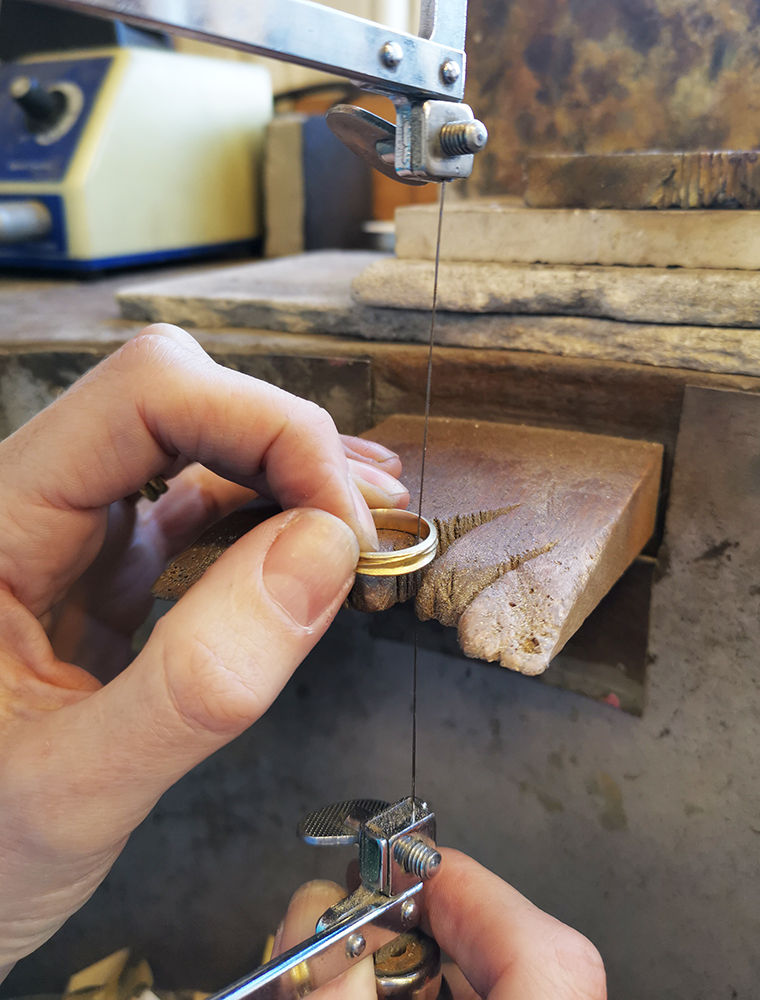
I use a fine-toothed saw to cut through the sprue. This is a really delicate process because I have to be very careful not to damage the rest of the ring.
Then, I defile and sand it, refining the finish to remove any rough spots or imperfections, ready for the next stage in the remodelling process.

Hallmarking the ring
With all of the cleaning up done, I’m ready to mark the ring up for hallmarking.
Hallmarking is when a specialist at the local Assay Office, which tests the purity of precious metals, will punch or laser engrave the inside of a ring to mark its quality and purity. It’s a reassurance for customers that the jewellery they buy is the real deal.
The hallmarking process that goes inside the jewellery has three elements:

- The sponsor’s mark - that’s me! It will say ‘KS’ to show who made it.
- The finesse mark - this shows what carat or what finesse the metal is - this ring is 18ct yellow gold so the stamp will read ‘750’, the mark for 18ct.
- An anchor to show it’s been hallmarked in Birmingham - each Assay Office around the country has a different mark so you can identify where a piece was hallmarked.
Setting the stones
Fresh from its hallmarking, the ring is now ready to go to our specialist stone setter.
Finding an excellent stone setter is a difficult task - you need a combination of reliability and skill. I have two I really trust. They have strengths in different types of setting, so who I choose depends on the project I’m working on.

Luckily, the one I’m using for this remodel is a two-minute walk from my workshop, so I’m back out to pay him a visit.
I go to him for a lot of our gem setting because he’s specially trained to do it - he does it amazingly well day in, day out, and I’m a firm believer in everyone playing to their strengths.

The finishing touches
Once the ring is back from the stone setter, it’s back to us to apply the final finishes. This involves polishing the setting edges and inside of the ring…
… before applying the final frosted finish to the outside of the ring.

The finished piece of jewellery
Ta-da! The ring is finally finished and it looks fantastic. I couldn’t be happier with how it’s turned out, and I’m so excited for my client to see it.

My client isn’t based locally, but she pays a visit to the workshop to collect the remodelled ring in person. It’s lovely to finally meet her in person after working so hard on her wedding ring and playing my own little role in her special day.
All that’s left for her to do now is transport her precious cargo home and hand it over to the best man for safekeeping until the day of the wedding. No pressure!
Talk to me about my jewellery remodelling service...
Hopefully, this blog post has given you an interesting insight into how my team and I at Kate Smith Jewellery breathe new life into old jewellery.
Personally, I believe remodelling is a wonderful way to honour memories, keep a little piece of the past alive, and craft a stunning new piece of jewellery in a conscious, sustainable way.
Do you have existing jewellery you no longer wear that you dream of turning into something you could wear and cherish every day?
I know it's hard when you have inherited jewellery that holds a special place in your heart but isn't to your taste. This is why I absolutely love to turn unworn jewellery into a unique piece with its very own story that you're proud to show off to the world!
Contact us on kate@katesmithjewellery.co.uk for a no-obligation chat or to book an appointment at my Birmingham Jewellery Quarter workshop and let's see what we can create for you.